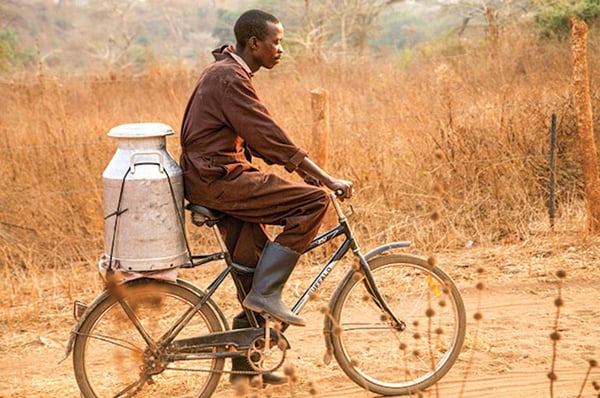
Emerging dairy sectors in developing African countries cannot cool raw milk on-farm due to the lack of reliable electricity. Often the quality of the evening milk is lost because it doesn’t survive the overnight heat.
A lack of knowledge of post-harvest practices combined with poor infrastructure and no storage facilities result in at least 40 percent milk waste. This creates a lost income opportunity for farmers and a growing gap between milk supply in African countries and milk demand.
Two companies, the World Bicycle Relief and the Paul Mueller Company, are making efforts to advance milk cooling in Africa by improving milk delivery, collection centers and on-farm storage.
Milk Delivery
One of the biggest challenges dairy farmers in Africa face is the reliable transportation of their milk to a centralized milk collection center. The distance is anywhere from 3 to 15 miles away from the farm.
Oftentimes, the milk is carried to these collection centers by low-grade bicycles, wheelbarrows or by walking.
“Many farmers were bringing milk on what I would call ‘inferior bicycles’ or what we call BSOs or bicycle-shaped objects,” says Dave Neiswander, president of World Bicycle Relief.
“These bicycles do not have the ability to carry 20- or 40-liter (5- or 10-gallon) canisters of milk to the milk collection center. They break down, so the reliability of transportation was not there.”
The World Bicycle Relief originally began providing bicycles in Africa to volunteer health care workers and rural students traveling long distances to school. The organization became interested in selling bicycles to dairy farmers when they saw their need for reliable transportation to deliver raw milk.
In 2010, Neiswander started working with dairy cooperatives in Zambia to provide Buffalo bicycles to dairy farmers with terms that were agreeable to them.
“We were able to work out a program where the milk cooperative would put together a list of farmers who worked with the cooperative on a regular basis,” Neiswander explains. “Through the program, the farmers are able to purchase the bicycles over a three-month period.
A deduction from the amount of money the cooperative is paying them monthly for their milk is taken out to pay for the bike.”
According to Neiswander, the Buffalo bicycle is a very strong robust bicycle made of steel that weighs roughly 45 pounds and can hold more than 200 pounds on the rear carrier.
“It is designed to stand against the difficult conditions and terrain that you find in the developing world,” Neiswander says. “Dairy farmers can rely upon the strength of the Buffalo bicycle to be a reliable transportation to take milk from their farm twice a day to the milk collection center.”
The unique difference between the Buffalo bicycle and regular bicycles is the rear platform, where dairy farmers can strap a milk canister.
“The ingenuity of those in Africa never ceases to amaze me,” Neiswander chuckles. “They will tie the canisters on with used tire tubes and strap them together and over the top.”
Neiswander says the World Bicycle Relief program has helped provide more than 400 bicycles in Palabana and more than 600 bicycles in Zambia by working through the different dairy associations and milk cooperatives.
As a result, Neiswander says they have seen an increase in deliveries which, in turn, has increased the volume of milk delivered. Farmer income has increased by 25 percent because of the Buffalo bicycle intervention.
Milk Collection
The Paul Mueller Company is also helping the African country of Uganda supply fresh milk to its citizens by installing milk collection centers. In the past, Ugandan farmers have only been able to collect as much milk as they could consume or trade within a couple of days. If the milk was not used within a few days, it would spoil.

When the problem for Ugandan dairy farmers was presented to Paul Mueller Company in the Netherlands, they knew just the solution. A team headed by Jos Ten Horn worked with the Dutch and Ugandan governments to receive funding for the construction and operation of the collection centers through grants.
The Ministry of Foreign Affairs issued grants to purchase Mueller steel milk tanks, cooling equipment, generators and heat recovery systems to set up milk collection centers in villages throughout Uganda. Peter Fopma, new business manager, says Mueller has sold and installed about 150 collection centers in Uganda so far.
The newly installed dairy collection centers contribute to less spoilage and better milk quality as milk is chilled in a few hours rather than the usual seven hours. Due to an increase in milk processing facilities and the project, local dairy cooperatives are able to increase their annual milk sales.
“It is making quite an impact, because when more milk is cooled, the collection center can make more products out of the cooled milk,” Fopma says. “This means the collection centers can pay a little more for the milk. If the farmers earn a little more for their milk, they will invest in their dairy and buy an extra cow, better feed or better semen.”
Milk Storage
Mueller has not built any milk collection centers in the country of Ethiopia because it is less developed than Uganda and has smaller dairy farms. Due to smaller herd sizes in Ethiopia, it is currently not economical to install collection centers because the milk tanks would not be filled completely.
“In 2011, BoP Innovation Center and LEI Wageningen University did a survey in Ethiopia and found that small-scale dairy farmers of one or two cows were not able to deliver the evening milk and make money from that milk,” Fopma says. “So Mueller was asked to develop an off-grid milk cooler for on farms.”
As a partner with BoP Inc., Mueller worked to develop a small cooling unit for small-scale dairy farmers in Ethiopia. The first prototype milk cooling unit they made was solar-powered and enabled small dairy farmers without access to electricity to store, deliver and sell the highest possible quality of milk and increase their income.
Fopma says while Mueller was working with BoP Inc., they came in close contact with a company called Simgas, which builds small biogas facilities for household farms in Africa. Simgas at the time was looking to add on to their system so, together with Mueller, they built a second prototype for a biogas-powered milk cooler in 2013.
Mueller’s goal for building the small on-farm cooling units in Ethiopia is to improve milk quality and enable farmers to sell their evening milk to double their income. His hope is that the farmers’ added income will increase herd size and milk production so larger milk collection centers can be installed in Ethiopia as well. 
To get involved, dairy farmers in the U.S. can visit the World Bicycle Relief website at world bicycle relief and help support the different programs assisting dairy farmers in Africa.
Audrey Schmitz was a 2016 Progressive Dairyman editorial intern.
PHOTO 1: Buffalo bicycles provide Zambia dairy farmers with reliable transportation to deliver milk twice a day to milk collection centers. Photo courtesy of Brooke Slezak.
PHOTO 2: Milk collection centers installed in Uganda contribute to less spoilage, better milk quality and maintain a supply of fresh milk to citizens. Photo courtesy of Christine Daues.