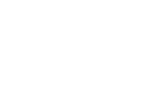
At Paul Mueller Company we are united by a belief that the only quality that matters is quality that works for life. With every piece of processing equipment we build, our goal is to have lasting impact. From solar milk coolers in rural Africa, to lifesaving medical technology we are making an impact across the globe.