If you find yourself facing heating or cooling challenges, custom heat transfer surface may be the answer.
Space-saving, Easy-to-Install Solutions
In many cases, custom Temp-Plate® inflated heat transfer panels are the best solution for passive temperature control of stored liquids. Immersed plate sections of spot-welded heat transfer can also provide a space-saving, easy-to-install solution. When talking about high pressures and temperature extremes, stamped dimple plate can be customized for any type of storage tank, shell, or cone and welded directly on, like a jacket. Finally half-pipe coil is appropriate for high pressure applications and low pressure drop requirements and it can handle large volumes of liquid. The versatility of custom heat transfer allows you to get exactly what you need to ensure efficient work flow, sustainable processes, and ultimately increased cost savings.
Temp-Plate® Energy Recovery Banks
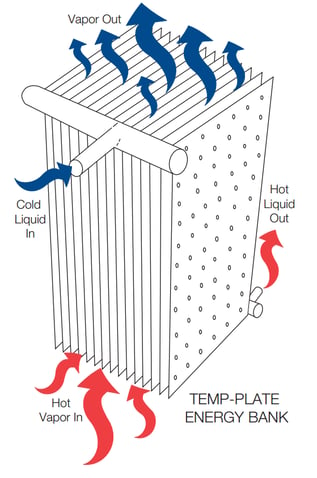
If your process vents exhaust into the atmosphere or loses heat in some other way, then Waste Heat Recovery provides an energy-savings solution by allowing you to capture the lost energy and reuse it. A processing plant in Alabama using thermal oxidizers to process the plant’s gas emissions in compliance with environmental regulations was experiencing a huge waste of high-grade heat when the exhaust gas from the oxidizers was being released into the atmosphere. At the same time, the plant was paying more than a million dollars each year for steam to heat their incoming process fluid. By installing a Temp-Plate energy recovery bank to capture the exhaust and use it to heat the steam, we were able to save them that million dollars year after year for a one-time cost of $460,000 (for installation plus equipment).
Projects in the field of condensation, evaporation or heat recovery that need high energy efficiency or feasibility in extreme conditions, can also take advantage of Temp-Plate energy banks. The chemical industry is seeing the benefits of condensing with Temp-Plate modules at low absolute pressure, a specialty developed by our German engineering company DEG Engineering GmbH. This case study shows how DEG's process knowledge combined with Mueller's Temp-Plate technology helped a refinery in India source efficient heat transfer equipment to provide very specific high heat loads, organized to an optimized flow geometry, producing high condensation rates.
Tanks and Heads
When you need to cool or heat the content of your tanks, our stamped dimple plate heat transfer surface is ideally suited for applications involving high pressure and temperature extremes. It can be routinely fabricated in an almost unlimited number of shapes, sizes, and materials to fit any vessel design. Styles are available for use with almost any type of refrigerant or heating media.
Half-pipe welded onto the outside of a tank head/shell is called a "half-pipe jacket. Mueller half-pipe coil heat transfer surface handles large volumes of flow and is suited for high-pressure applications as well as low-pressure drop requirements. It is ideal for cyclic heat transfer conditions in which heating and cooling cycles occur several times a day as it is very resistant to stress corrosion cracking. Half-pipe coil is used for heating or cooling with steam, hot oil, water, glycol, ammonia, and refrigerants. ASME code stamping is available.
Machine Oil Cooling
In machining processes, oil is commonly used as a lubricant or cooling medium. Oil is also very susceptible to contamination, and, due to its effectiveness as a cooling medium, becomes hot easily. Generally, a traditional shell-and-tube heat exchanger is used to remedy this issue but comes with its own set of issues. Since shell-and-tube heat exchangers are difficult to clean, dirty oil will render them useless over time requiring constant maintenance.
Since a tank is much easier to clean and take out of service, the best solution to this issue is to run the dirty oil through a holding tank so that the contaminants can settle to the bottom preventing the outflow from clogging a heat exchanger.
This assembly also includes a tank to filter the oil before running it through the heat exchanger. The problem is that this is more expensive because it involves an additional component. However, by using Temp-Plate panels in the form of an immersed plate or a tank jacket, it would be possible to have the functionality of a heat exchanger at a much lower price point without the risk of clogging.
Two of our customers, a Tennessee chainsaw blade manufacturer and a Missouri-based clay pigeon manufacturer, used Temp-Plate in this way to improve their efficiency. The Tennessee company passed their cutting oils through a tank fitted with a bank of immersed Temp-Plate sections and used an agitator to keep iron filings in suspension. This allowed them to avoid cleaning them out manually. The Missouri company ordered custom shapes of Temp-Plate to facilitate an intermediate fluid (ethylene glycol), preventing dirty oil from plugging up their process. By using the Temp-Plate in conjunction with an existing heat exchanger, they were able to easily clean their system which significantly reduced downtime.
While machine oil cooling is a common application, this kind of solution works in any case where particulates can impede your process stream.
Clamp-On Applications
One of the applications that makes custom heat transfer so versatile is the clamp-ons, where standard or custom-sized plates can be clamped on to a vessel. The greatest benefit of a clamp-on application is how easy it is to install within an existing process. Sometimes, as a process evolves, the need for a heat exchanger develops, but the floor plan may not have sufficient room for one. In this case, custom heat transfer can be clamped on to an existing vessel to serve as a heat exchanger without taking up any extra space.
Becon Engineering from Houston serves as a great example of this application. Becon was working on a project for Chevron, which required hot water for a demineralized water dilution heater in the middle of the oil refining process. Because there was no nearby power source available to supply the hot water, Becon clamped 51 square feet of Temp-Plate to a 14” high pressure steam line – the only available heat source. In this case, Temp-Plate offered an engineering firm the flexibility to economically solve an otherwise expensive problem.
Another advantage of Temp-Plate is that it can withstand very high pressures (up to 1500 psig). Brown & Root Engineering, another customer from Houston, needed to keep a salt storage tank at 400ºF with 600 psig steam at 486ºF. With the right specifications, Temp-Plate achieved those marks easily.
Conclusion
Sometimes, heat exchange processes require creativity, and Paul Mueller Company Temp-Plate, dimple plate and half-pipe coil provide flexibility and cost-savings for custom heat transfer solutions in various applications.
Contact us today to start designing your custom heat transfer process.
Additional Resources:
If you found the above applications interesting, check out these other application for Heat Transfer.
Open Heart Surgery:
During open-heart surgery, the heart is stopped. In order to avoid damage to vital organs, cold water is created in a heater-cooler device and used to regulate body temperature.
Heat Recovery in a Plant:
Sustainability is goal for many large companies. How to achieve that goal is sometimes a tough thing to figure out. See how one chemical company partnered with Paul Mueller company to address the situation and saved $1 million.
Hydrocooling:
When it comes to fruits and vegetables, freshness is among the highest priority. Once picked, the clock starts on capturing that freshness. Hydrocooling is among one of the fastest ways to cool produce but also very efficient.
Drum Drying:
Dry ingredients are the foundation of some products. Removing all the moisture can be a very inefficient process. Temp-Plate panels are a component added to these dryers to use only the amount of steam necessary to dry your ingredients to perfection and send money back to your bottom line.