With the increased demand for high-quality dairy products, dairy farmers are using new technologies to ensure their milk remains fresh before it is sent for dairy processing or delivered to consumers. Among these innovations, pipe coolers have stood out as a game-changer in the dairy industry. They not only enhance the quality and shelf life of milk but also streamline the process of cooling milk.
Pipe coolers play a crucial role in preserving its nutritional value and taste by quickly reducing the milk’s temperature immediately after extraction. This technology has improved dairy production, leading to a future where freshness and efficiency can go hand in hand.
What is a Pipe Cooler and How Does it Work?
A pipe cooler, also known as a pipe heat exchanger, is a device designed to pre-cool milk before it enters the milk tank. The principle behind its operation is the counter-current principle in which milk and cold spring water flow in separate channels and in opposite directions. This allows for efficient heat exchange, promoting rapid milk cooling.
Benefits of Using Pipe Coolers
1. Enhanced Milk Quality
Maintaining milk quality is critical for both consumer safety and the economic success of dairy operations. Milk that's poorly handled can lead to bacterial growth, spoilage, and health risks, including foodborne illnesses, nutritional degradation, and economic loss from reduced shelf life. Strict processing standards, such as pasteurization and cooling, are essential to ensure milk quality. Pipe coolers play a key role by quickly cooling milk after harvest, preventing bacteria growth, improving quality, preserving nutrients, and prolonging shelf life.2. Increased Efficiency
Mueller Pipe coolers effectively cool milk before storage, enhancing energy efficiency by reducing the need to maintain low temperatures. The Mueller Pipe Cooler lowers electricity costs and benefits the environment by doing so. Farmers often use borehole water, which is also suitable for cow consumption, in these coolers to pre-cool the milk. The warmed water, a byproduct of this process, is given to cows, which is particularly beneficial during colder winter or hot summer days, as cows prefer slightly warmer water. Under warmer conditions, cows can drink enough water in a relatively short period. As a result, the Mueller Pipe Cooler emphasizes a commitment to using resources wisely and sustainably. Additionally, incorporating pre-cooled milk into the production process streamlines operations, minimizes delays, and enhances overall output.3. Energy & Cost-Savings
In dairy operations, managing energy and costs is paramount. Pre-cooling milk after collection reduces the energy needed for refrigeration, cutting energy use, keeping milk fresh, and lowering spoilage risks. This strategy leads to cost savings by maintaining milk quality and stabilizes milk temperatures, making dairy processing more efficient.The Mueller pipe cooler excels in pre-cooling milk using cold water or glycol for heat transfer. This significantly reduces dependence on electrical refrigeration and promotes coolant reuse, thereby cutting energy consumption by up to 45% and yielding substantial cost savings over time. Designed for dairy farms of any size, it optimizes energy use and can cut energy consumption by half, offering significant cost savings.
4. Space Savings
In scenarios where spatial constraints limit the adoption of plate coolers, pipe coolers stand out for their compact and efficient design. They afford dairy farms the ability to harness the benefits of pre-cooled milk without requiring significant space, thereby accommodating even those with stringent spatial limitations.The vertical configuration options of some models can make use of otherwise underutilized space, maximizing the efficiency of the available floor area. Additionally, the modular nature of pipe coolers supports scalable expansions without imposing substantial spatial demands, thus enabling streamlined, space-efficient dairy processing facilities capable of adapting to growth and operational shifts seamlessly.
5. Hygiene
Design of the Mueller pipe cooler is based on as low as possible pressure drop during cleaning. During cleaning the milk pump (parlor/robot) is having a minimum pressure drop to push the cleaning water through the milk pipes or pipe cooler.
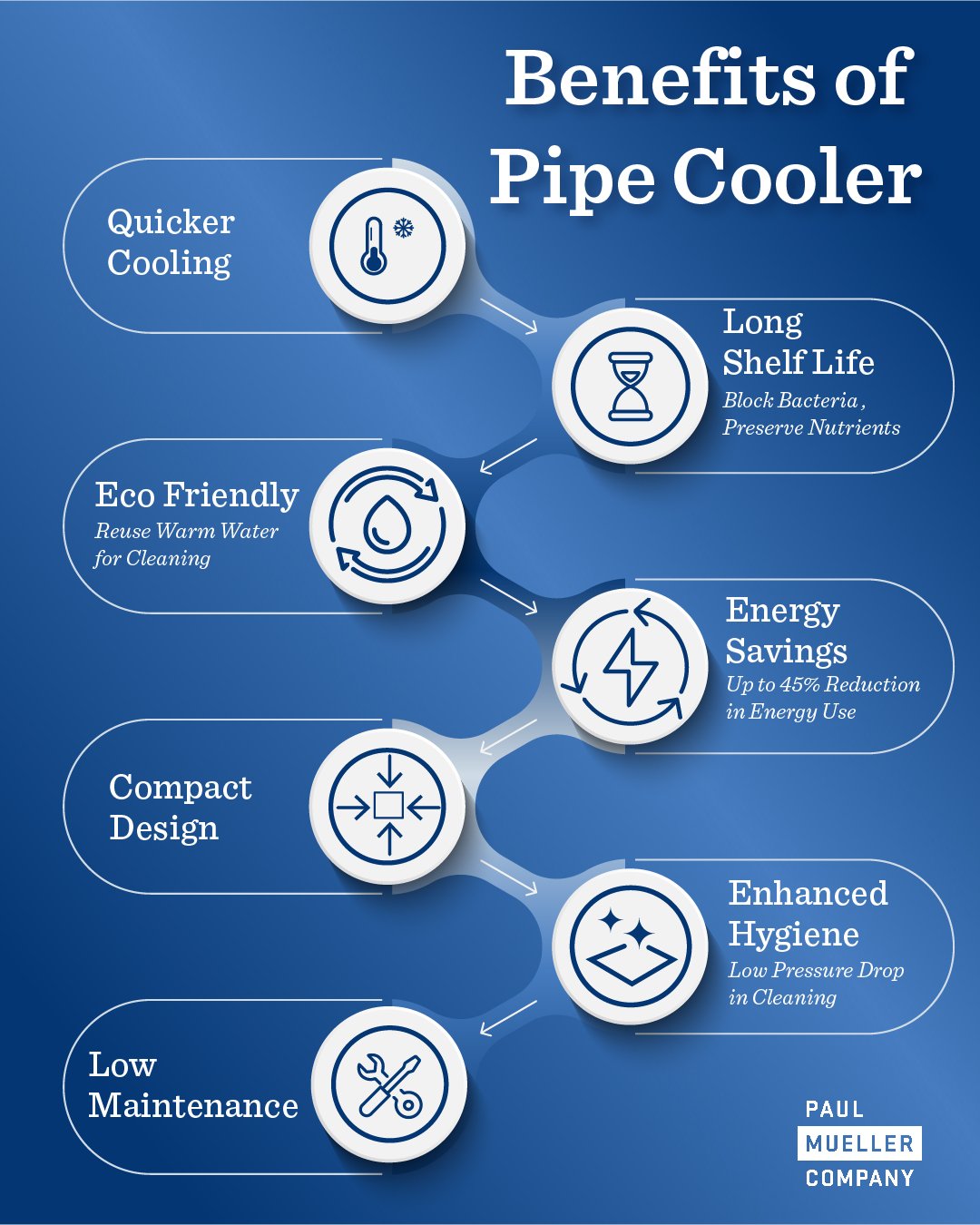
Pipe coolers represent a crucial innovation in dairy farm management, offering a multifaceted approach to improving milk quality, enhancing operational efficiency, achieving energy and cost savings, and space utilization. Their role is indispensable in modern dairy operations, ensuring the production of safe, high-quality milk while also addressing economic and environmental considerations.
Choosing the Right Pre-Cooling Option
While pipe coolers are highly effective, it's essential to consider factors such as milk flow when selecting the right pre-cooling option for your operation. At Paul Mueller Company, our dairy farm equipment experts can help assess your farm's needs and recommend the most suitable solution.
The choice of an optimal pre-cooler type largely depends on the milk flow. A single pipe cooler can cool up to 3000 liters per hour, and a duo pipe cooler can cool up to 6000 liters per hour. As a result, for larger operations, a plate cooler may be a great option.
Paul Mueller Company Personalized Energy Audit
Interested in maximizing milk quality while minimizing energy costs? Reach out to our milk cooling experts for a personalized energy audit. We'll evaluate your farm's setup and provide insights into potential savings opportunities.
Optimizing milk cooling processes is key to maintaining quality standards and achieving cost-efficiency. With pipe coolers from Paul Mueller Company, you can achieve both goals simultaneously. Invest in the future of your dairy operation by incorporating efficient milk cooling solutions today.